Leuze sensor offers measuring and switching
18th March 2022
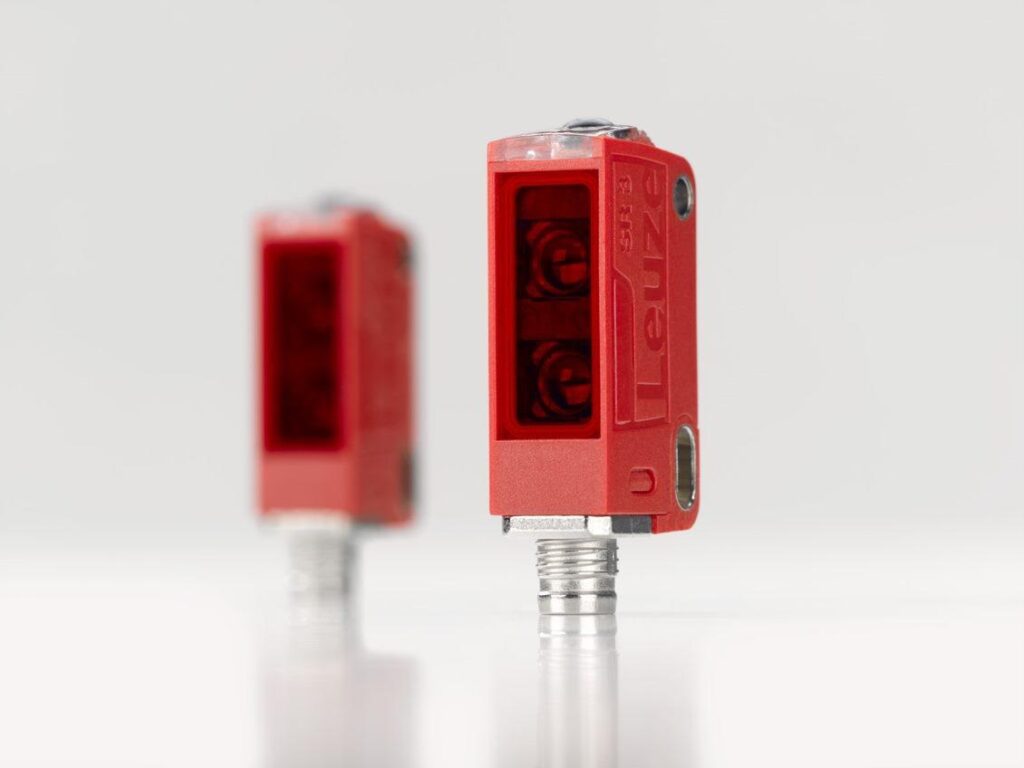
The innovative ODT 3C sensor from Leuze can handle both measuring and switching tasks. The new 2-in-1 solution is thus suitable for a wide range of automated industrial applications.
Is there an object on the conveyor belt? If yes: What is its position or distance to the machine? These are typical issues that need to be addressed in a wide range of industrial applications and processes. In the past, to solve this problem required the use of multiple sensors. With the new ODT 3C from Leuze, only a single device is needed: The innovative sensor can transmit both switching and measuring information to the machine control system, which makes it an efficient and economical 2-in-1 solution.
Flexibility with a single sensor
The ODT 3C transmits measurement values and extensive diagnostic data via IO-Link. The data includes temperature values, warnings, and signal quality. It features impressive black-and-white behaviour (< ±3mm at 150mm). The operating range can be easily adjusted via the teach button, remote signal or IO-Link.
The new Leuze sensor also offers impressive functional reliability: Active ambient light suppression prevents faulty switching, even when exposed to direct light from LED building lighting systems. LEDs that are easily visible from all sides allow you to quickly read the status of the ODT 3C. Two independent switching outputs and sensor models with warning output or a small light spot (pinpoint) round of the sensor’s functions. This enables plant operators to use the ODT 3C flexibly in a wide range of applications.
Application example from food industry
A machine is rolling off dough for baked goods. The ODT 3C sensor is pointing down onto the dough. It sends a distance value to the parent control. The goal is to regulate the dough within an optimal distance range of 100–120mm.
If the sensor detects a measurement value outside the target range, the conveyor belt motors adjust the speed of the conveyor accordingly. The measurement value is evaluated in the process data via IO-Link. In addition, diagnostic data is transmitted to the controller via IO-Link for Industry 4.0 purposes.